The workforce of the future: how will technology impact the manufacturing industry?
Learn how to build a manufacturing enterprise with strategic human intelligence in order to stay competitive and turn disruption into opportunity.
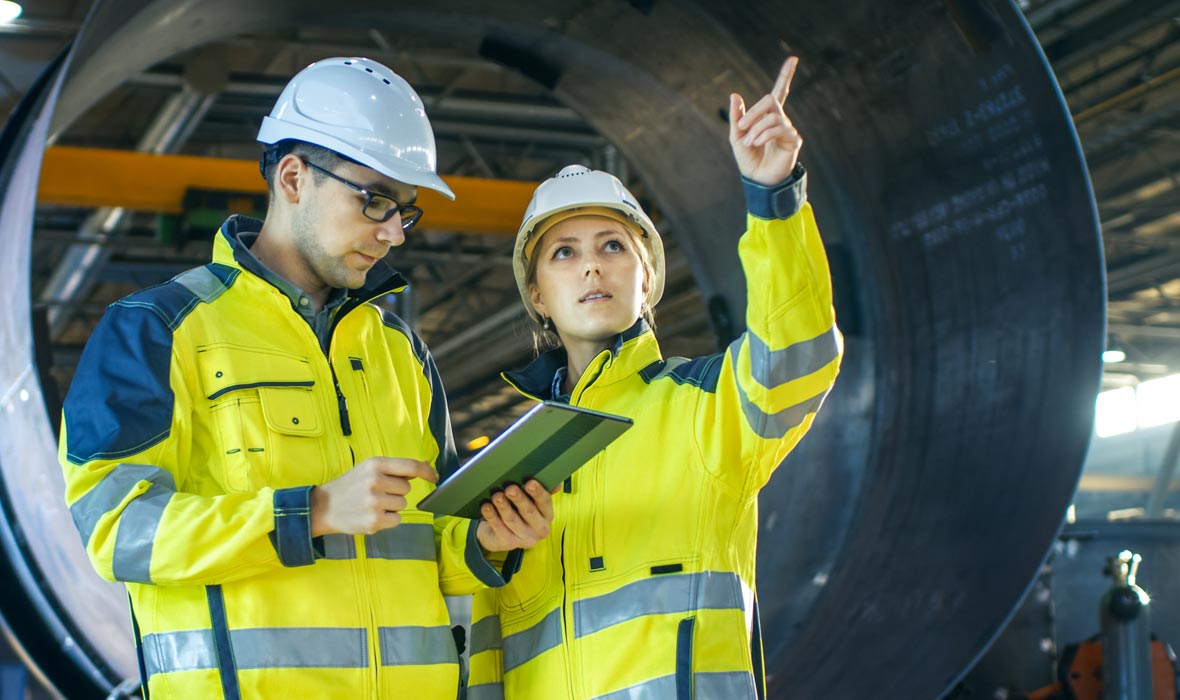
Disruptive innovation is here to stay
Disruptive innovation is becoming a very real part of the manufacturing industry. In fact, adoption rates of advanced technologies indicate that most of America’s factory floors are already in a disruption cycle. As costs decline and capabilities improve, artificial intelligence (AI) and other automating technologies are now set to reconstruct the manufacturing industry.
In the recent McKinsey Global Institute report, Jobs lost, jobs gained: Workforce transitions in a time of automation, they found that by 2030, as many as 375 million workers — or roughly 14 percent of the global workforce — may need to switch occupational categories as digitization, automation, and advances in artificial intelligence disrupt the world of work.
According to a recent survey of 1,600 global enterprises, 71 percent of industry leaders expect widespread adoption of AI and robotics in the near future.
As the nature of work changes, organizations need to create new strategies to augment human intelligence in order to stay competitive.
Turning disruption into opportunity
Computer automated systems now work faster and more reliably than their human counterparts, performing tasks beyond human capability. AI-driven technologies like virtual assistants, automated checkout systems, driverless cars, and fraud detection technologies, are already becoming commonplace. At the same time, AI and other disruptive technologies are still constrained by significant limitations, and this has important implications for how we think about education and the future of skilled labor.
As Rana Foroohar from the Financial times stated, “A way for companies and government to turn a potential employment disaster into an opportunity by using this disruption to train a 21st-century workforce and build the public infrastructure to support it.”
Notwithstanding the fact that advanced AI and machine learning could begin displacing much of the global workforce over the next two decades, there remain substantial opportunities for advancing the skills of workers. As a recent report by the McKinsey Global Institute indicates, the hardest activities to automate are those activities involving complex expertise in decision-making, planning, human interaction, imagination, and creative work. Put simply, although machine learning has been particularly effective at making predictions, it has been much less successful at managing challenges associated with judgment, decision-making, and interpretation.
Building a manufacturing enterprise with strategic intelligence
Building and maintaining a successful manufacturing enterprise requires more than just technology. It requires strategic human intelligence.
As Deloitte observes, high-performance organizations are becoming empowered networks, coordinated through culture, information systems, and talent mobility.
With the digital transformation underway, companies are focused on redesigning the organization itself. As networks and ecosystems replace organizational hierarchies, organizational learning is becoming the platform upon which emergent organizations evolve and mature.
Organizational learning and high-performance
In order to be a high-performance organization and address the importance of talent mobility, companies must make strategic investments in their learning ecosystems, determining where the greatest skill gaps exist and what resources are available to fill those gaps. Unfortunately, in companies where human resources (HR) departments are solely responsible for employee development, gaps between strategy and execution become evident.
Companies now need to continually integrate new skills into their feedback loops, to better join HR strategy with an organization’s overall capacity for organizational learning.
As the manufacturing industry begins to shift around smart design and smart factories, manufacturers and designers will need to incorporate learning impact into their business planning.
Learning impact in the manufacturing industry
Learning impact occurs when skills learned are applied in the workplace, then improve performance and drive business goals. The knowledge value-chain is a sequence of intellectual tasks by which a worker’s knowledge builds an employer’s unique competitive advantage. Even as learning is consumed on an individual basis, the value comes when it is retained. It adds further value when the individual remembers what they have learned, and apply it at the appropriate time in the appropriate context in the workplace.
Now imagine if 10,000 workers are making even the subtlest of improvements in performance. 10,000 improvements accumulate, and it equates to progress to achieving business outcomes.
Embracing the imagination economy
Even as new waves of automating technologies displace a wide range of occupations, it remains the case that technology is complementary to many kinds of creative work. In fact, these technological trends are giving rise to what many thought leaders refer to as the “imagination economy“. That is, an economy where intuitive and creative thinking creates economic value, even as logical and rational thinking are increasingly automated.
Even as the manufacturing sector undergoes a technology renaissance, leaders must focus on developing ever-closer linkages between research and development (R&D), data analytics and product design. But they must also consider significant improvements in systems for advancing human capital. Learning and training must now be closely aligned with continuous improvements in the manufacturing process itself. Learning and doing are becoming increasingly interactive. This means:
The future of the manufacturing industry
Globally, manufacturing continues to grow. It now accounts for approximately 16 percent of global GDP and 14 percent of employment. As factories adopt new technologies in order to increase productivity and reduce costs, AI and 3D printing are making it easier for manufacturers to experiment with new product designs and create intricate composite parts. All of this means that learning and doing are much more closely integrated than in the past.
The need to augment learning throughout the manufacturing sector has now made organizational learning critical to driving growth. As companies invest in scalable HR reporting and workforce analytics solutions, they can also begin to understand what to measure and how those measures can impact their workforce and their business outcomes. A new breed of learning technology must advance, alongside AI and robotics, leveraging AI and virtual/augmented reality (VR/AR), to enhance corporate learning.
Learning is a business strategy
Organizational performance is now increasingly centered on how learning and training efforts translate into real business results. The only way to measure organizational learning is with performance data that is analyzed and tracked by technology. Investing in workforce analytics enables leaders in the manufacturing industry to better evaluate the health of their organizations. It is necessary to tie learning metrics to business goals and communicate success at the executive level.
L&D tools that support segmentation analysis, correlation and regression analysis, enable leaders to continually evolve the organization as a whole. Key performance indicators (KPIs) help to determine whether a given business has sufficient skills to arrive at required business objectives. Regardless of time, place, or particular device, organizations require effective solutions for the management and monitoring of organizational L&D systems, providing detailed data analytics supporting learning outcomes.
Adapting with learning
As technology life cycles accelerate, qualifications are becoming obsolete more quickly, hastening the need for organizational investment in lifelong learning systems. Corporate leaders are now challenged to adapt to this new environment and as these leaders begin to accept that disruptions to their business models are inevitable, continuous personnel education and training will become routine. In fact, organizational learning as a part of company strategy will become the norm. For this reason, data-driven analytics now play a key role in advancing strategic outcomes.
Manufacturing remains a critical force in the global economy but the sector has changed. Educational requirements for occupations will continue to grow, and that means ever-greater investments in L&D. Even as cheaper, more capable technologies accelerate the growth of automated manufacturing systems, companies will need to harness their human resources to innovate.
The benefits of a learning platform in the manufacturing industry
The manufacturing industry can benefit from a learning platform to retrain employees and minimize costs. For example, a large Finnish company in manufacturing trained and retrained their external contractor network, subcontractor network and reseller network with the learning experience platform, but was white-labeled according to their own brand to better drive engagement.
The training affected a global network of contractors and resellers in over 90 countries. Not only did the training cut costs, but the training was more effective because the company originally had all of their courses in a printed catalogue, and they would also fly to Finland for courses. In addition to in-person training, the new company training environment offered these external networks the chance to learn from anywhere in the world, whenever they wanted to. The flexibility in training is easier to scale and easier to manage.
As disruptive technologies like AI become even more commonplace, organizational learning that supports imagination and creativity will determine who leads the future of manufacturing in the 21st century.