Measuring competence enables data-driven management
Stay ahead of the competition by measuring employee competence, then link it to effective learning and your key business performance indicators.
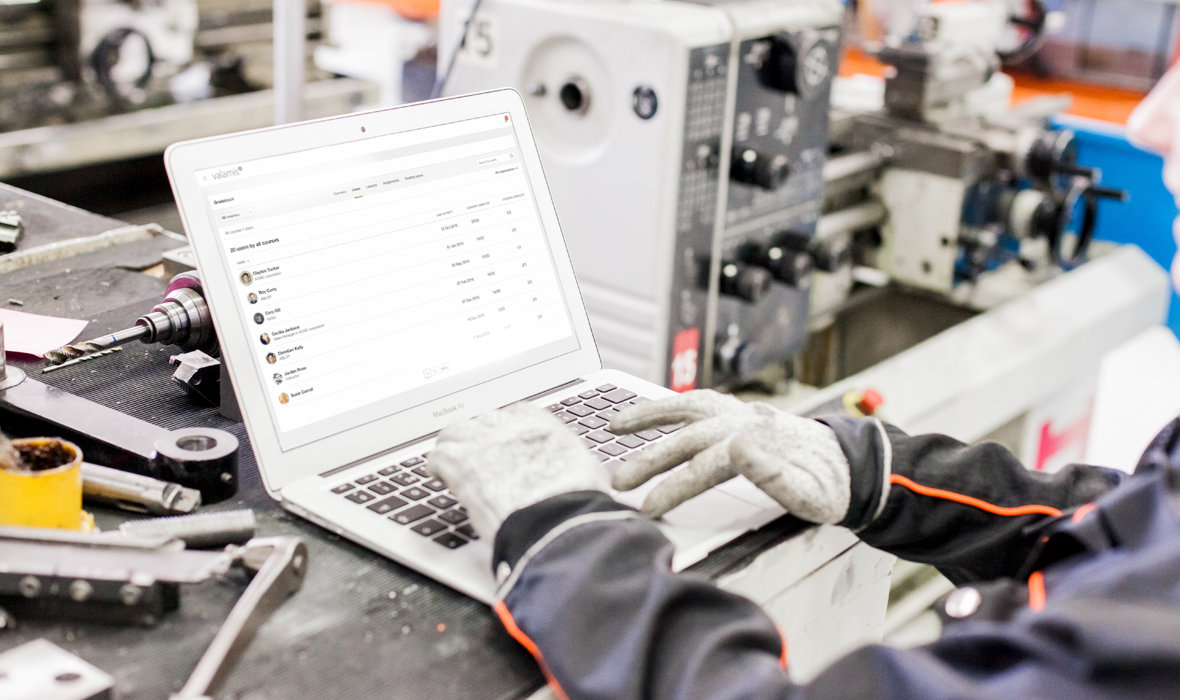
Digital learning environments enable data-driven management of extensive networks in new ways. Are you familiar with the competences of your company and your subcontractors? Do you measure them? Linking the effectiveness of learning to business performance indicators is possible when the competence indicators are accurate enough.
Management based on results and gut feeling is a thing of the past, even in the traditional manufacturing sector. The manufacturing boom is increasing the number of personnel throughout the supply chain. Success in the face of intensifying competition requires that companies and their extensive networks of subcontractors and retailers are managed with data insight.
Professor Amy Edmondson from Harvard Business School and Learning Engineer Bror Saxberg argue that the value of a company can’t grow without investing in the lifelong learning of its employees. The source of competitive advantage in the future will be skilled people, not machines (McKinsey Quarterly, September 2017).
In manufacturing, it is essential for management to have insight not only into the skills and strengths of the organization’s own employees but also the competence of its network of suppliers and retailers. As many customers only come into contact with retailers and after-sales service providers, these network members are an important part of the brand. It is essential for a company’s growth and development that the broader network has the necessary competences up-to-speed.
It’s not enough to simply monitor and measure sales figures or other such outcomes.
The only way to stay ahead of the competition, is and will be to measure employee competence and to link the effectiveness of learning to your business performance indicators. Measuring competence makes it possible to make more accurate forecasts, which is important for business objectives.
Measuring competence is promoted by digital learning environments, such as the Valamis – Learning Experience Platform. When management is committed to measuring competences, the entire organization and its networks benefit from using a digital learning platform.
The challenge: Learning materials rapidly become outdated
Manufacturing is a cyclical sector. Major seasonal variations in production and employee volume create the need for continuous training and development of competence.
Providing training to an extensive network takes considerable time and resources. There is a great need for streamlining this process. Because reliable delivery and quality depend greatly on the level of competence, manufacturers invest in training.
Training that is provided using current models can take as long as two years because it is delivered at different times in different units and countries. The learning materials can even become outdated before the training has been completed if the rate of product development exceeds the rate at which training is provided. Training costs increase if training providers are flown from country to country. Outdated information is costly when it leads to lower quality and product recalls.
Recalling products in Brazil or servicing equipment locally is a setback that no company wants. Nevertheless, it can easily happen if the organization is not up to date on the competences of its various units and employees.
The solution: High quality and measurable training methods
The preconditions for success in manufacturing, such as reliable delivery, are inextricably linked to employee competence. Given that the perception of quality is essential in manufacturing, companies can’t afford to make mistakes.
One important way of avoiding mistakes is to use a more effective training method.
Reliable and high-quality operations are possible only when all members of the network have access to the latest information at the same time. Management must be able to ensure that the entire network has updated its competence in accordance with new methods and product changes. Digital platforms make this possible.
At the same time, it marks a step towards data-driven management.
Switching from folders and paper-based training materials to a digital learning platform makes data visible.
Switching from folders and paper-based training materials to a digital learning platform makes data visible. A learning platform gathers data that can be used to measure competence and evaluate training needs. A learning platform makes it possible to trace competences, and to find the best knowledge and skills available in the organization. Targeting of training resources will be better justified when there are well defined measures of competence.
An effective training method motivates employees. Up-to-date skills and competences make work more fluid and increase the efficiency of production. Everybody wins.
Achieving change starts with recognizing competence as a key metric from the business perspective.
Management has a key role regarding the importance of employee development. It’s essential for management to commit to using the digital learning environment and measurement of competence to ensure that the new way of learning is effectively deployed throughout the organization and its network of suppliers and subcontractors.
The outcome: Certified professionals
Provision of training to an organization and its extended networks can no longer take years to complete. Products and methods change rapidly, creating an ongoing need to keep methodological competencies current. An effective training method is a competitive advantage. A digital learning environment enables an international organization to distribute its training materials across multiple continents at the same time. Production efficiency is improved when the information is deployed simultaneously throughout the production chain.
Our customer Planmeca, a manufacturer of dental care equipment, has also put the Valamis platform to good use. The use of the digital learning experience platform has helped improve the reliability of Planmeca’s equipment, and has consequently increased its customer loyalty.
When learning takes place in a digital environment, the company can measure the level of employee competence throughout the network and manage its business more rationally with data insight.
Read also: A. Edmondson and B. Saxberg, 2017: “Putting lifelong learning on the CEO agenda”.